Fascination About Manufacturing Industriess
Wiki Article
The Ultimate Guide To Die Casting
Table of ContentsEverything about Lean ManufacturingExcitement About Hon Hai PrecisionThe Greatest Guide To ManufacturingSome Known Factual Statements About Oem
With injection moulding, pre-dried granular plastic is fed by a forced ram from a receptacle into a warmed barrel. As the granules are slowly progressed by a screw-type plunger, the plastic is required right into a heated chamber, where it is melted. As the plunger advancements, the melted plastic is required with a nozzle that rests against the mould, allowing it to go into the mould dental caries through a gate and jogger system.The series of events throughout the injection mould of a plastic component is called the injection moulding cycle. The cycle starts when the mould closes, complied with by the injection of the polymer right into the mould cavity. Once the tooth cavity is filled, a holding pressure is maintained to compensate for product contraction.
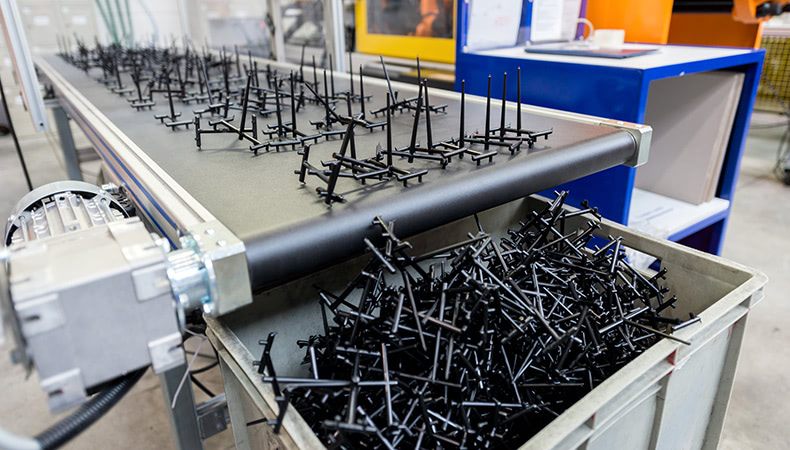
When the cavity is 98% complete, the device switches over from velocity control to pressure control, where the cavity is "packed out" at a consistent pressure, where sufficient speed to get to preferred pressures is called for. This lets workers manage component measurements to within thousandths of an inch or much better. Like all commercial processes, shot molding can generate problematic parts, even in playthings.
The Basic Principles Of Oem
Tests are usually executed prior to complete production runs in an initiative to forecast problems and also establish the ideal requirements to use in the shot process.: 180 When filling up a new or strange mould for the very first time, where shot size for that mould is unidentified, a technician/tool setter may carry out a dry run before a complete manufacturing run.
Holding stress is boosted up until the components are without sinks as well as component weight has actually been attained. Molding issues [modify] Injection moulding is a complex technology with feasible production issues. They can be triggered either by flaws in the moulds, or regularly by the moulding process itself.: 4785 Moulding problems Alternate name Descriptions Causes Blister Blistering Raised or layered area on surface of the part Device or product is too warm, commonly triggered by an absence of cooling down around the device or a damaged heating system.

Some Known Details About Plastic Manufacturing
Installed particulates Foreign fragment (scorched material or various other) ingrained in the part Particles on the device surface, polluted product or international debris in the barrel, or as well much shear warm melting the product before shot. Flow lines Directionally "off tone" wavy lines or patterns Injection speeds too slow (the plastic has cooled off excessive throughout shot, shot rates need to be established as quick as is ideal for the procedure as well as material utilized).Loading also fast, not permitting the sides of the part to establish. Additionally mould might run out registration (when both halves don't centre properly and component walls are not the very same density). The offered info is the usual understanding, Correction: The Lack of pack (not holding) stress (pack pressure is used to load out even though is the component throughout the holding time).
In other words, as the component diminishes the material separated from itself as there was not enough resin in the dental caries. The space could occur at any location or the part is not restricted by the thickness yet by the material flow and also thermal conductivity, yet it is most likely to occur at thicker areas like ribs or managers.
Knit line/ Blend line/ Transfer line Discoloured line where two flow fronts satisfy Mould or material temperatures established too reduced (the material is cool when they satisfy, so they do not bond). Time for transition in between injection and also transfer (to packing as well as holding) is too early. Twisting Altered part Air conditioning is also brief, material is too warm, lack of cooling down around the tool, incorrect water temperatures (the components bow inwards towards the hot side of the tool) Uneven reducing between areas of the part.
The Greatest Guide To Oem
125 inch wall density is +/- 0. 008 inch (0. 2 mm).: 446 Power demands [modify] The power required for this procedure of injection moulding depends upon this contact form numerous things and differs in between products used. Manufacturing Processes Reference Guide mentions that the power needs depend on "a material's details gravity, melting factor, thermal conductivity, component dimension, and also molding price." Below is a table from page 243 go right here of the exact same referral as previously pointed out that best illustrates the attributes appropriate to the power needed for the most frequently used materials.In enhancement to placing assessment systems on automatic gadgets, multiple-axis robotics can remove components from the mould as well as position them for additional processes. Details circumstances consist of removing of parts from the mould promptly after the components are produced, along with using machine vision systems. A robotic grips the component after the ejector pins have been included free the part from the mould.
Why is shot molding maker manufacturing so reliable? As well as how does it function? To discover, allow's dig right into the subject as well as address all of the crucial concerns, including what it is, the process behind it, its primary benefits, and also exactly how to pick the ideal provider. What is Injection Molding? is the procedure of using plastic to manufacture a vast array of components and also things.
The shot molding machine utilizes customized molds to fill them out according to specs, developing identical copies that can be personalized in a variety of methods. What's even more, injection molding is a very flexible process, enabling a wide range of different materials and surfaces, that makes it a preferred alternative in numerous her latest blog sectors with completely various objectives and also requirements - oem.
Report this wiki page